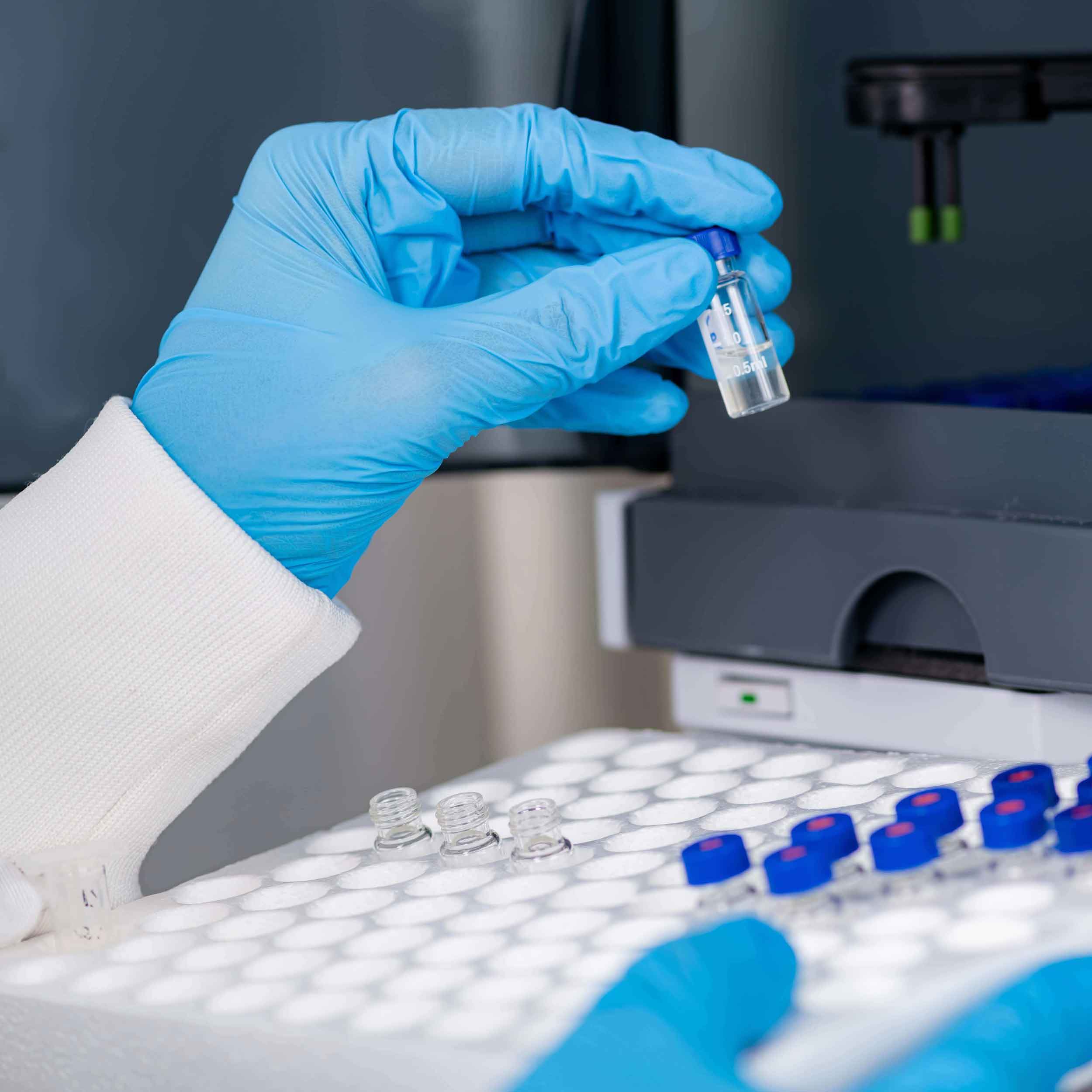
Aug 20, 2020
Quality Control (QC) in a laboratory setting is critical to ensure the accuracy of results used to deliver diagnostic information to patients. Aside from being a requirement, labs are constantly vigilant in ensuring the accuracy of their results, procedures and training
QC programs in a laboratory setting touch 11 crucial elements :
The laboratory must be organized around a formal quality management system that supports consistent procedures. The management team and quality unit play an integral role in a quality-driven culture, along with structures for monitoring ongoing quality.
The personnel must be capable, qualified and are the single most important asset to a laboratory. Training, motivation, and engagement are key parts of the quality management system. All training processes need to be documented within the quality management system.
Every piece of equipment used in the laboratory should be maintained to operate safely. The lab personnel need to monitor how equipment is installed, which suppliers provide the equipment, any calibration processes, and when the equipment needs to be replaced to maintain the highest possible quality.
Properly managing the supply chain is critical to ensure that raw inputs and other supplies are consistently high-quality. Inventory activities will ensure that materials and supplies are stored in a way that protects integrity. Need to ensure that inventory is purchased from suppliers who also follow a quality management system.
Process control encompasses QC processes for testing, including:
• Collection
• Handling
• Method Verification
• Process Validation
The laboratory must maintain many forms of information, including QC test results, maintenance reports, and other data. Along with that, the lab processes patient information such as diagnostics results. This data should be managed in a way that ensures all information is accurate, secure, confidential, and accessible to individuals with the right privileges, such as lab managers and leadership.
One of the most essential lab documents is standard operating procedures (SOPs) to create a standard for each process. Documents shall be made available at the point of work, maintained, accurate, and secure using a document management system.
An “occurrence” is any error or non-conformance. A QMS software can help you detect these issues and facilitate investigations to discover the root cause and prevent reoccurrence. A laboratory QMS can also assist you if you’re going through an audit, as it’s much easier to document these occurrences and what you did to fix them.
Assessment involves comparing laboratory performance to internal standards for quality or external data sets, such as industry benchmarks. Assessments include the activities of lab or QC managers, internal auditors, or external inspectors.
A quality management system should support the continuous improvement of laboratory processes. Components of the QMS which support improvement can include quality assurance, quality control, and CAPA (occurrence management).
Customer service is the ultimate goal of a laboratory. A laboratory’s QMS should support operations that consistently provide a positive customer experience through the production of consistently high-quality products or other missions. The laboratory needs to understand the customers and their needs and use customer feedback for improvement.
Laboratories need a comprehensive set of procedures and standards to ensure a safe, secure, and clean environment. This includes physically securing the lab, containment procedures for hazards, worker safety, and ergonomics.